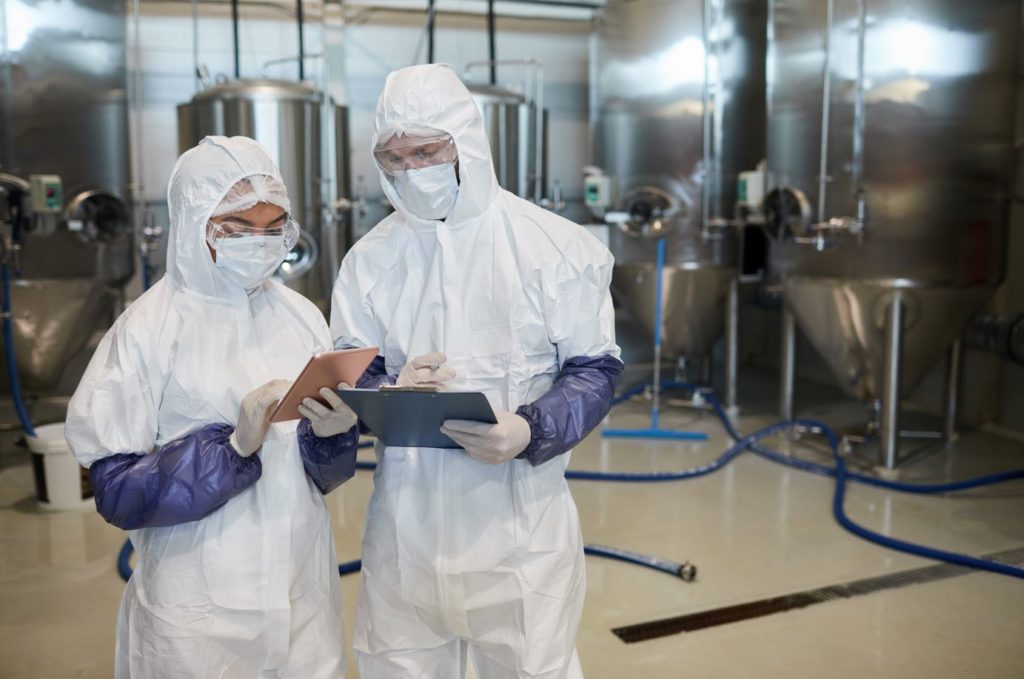
Perché le aziende dovrebbero aumentare l’effort in fase di Commissioning?
Articolo a cura del Team Qualifiche S4BT
Non esiste più una netta distinzione tra Commissioning e Qualification. Questo secondo la tendenza degli ultimi anni in cui sono stati integrati i nuovi approcci alla qualifica dei sistemi di produzione, dettati dalle linee guida e normative internazionali.
Nell’ambito del graduale abbandono del classico modello a V, che prevede anche l’uso del leveraging dalle fasi di commissioning, oggi Commissioning e Qualification (C&Q) vengono integrati creando un unico processo. Ciò grazie al coinvolgimento maggiore delle Good Engineering Practice (GEP), i cui principi vengono utilizzati per sviluppare test di qualifica mirati a stabilire se un impianto, sistema o equipment sia adatto allo scopo per cui è stato progettato.
Approccio Risk Based in fase di Progettazione
Il nuovo approccio di testing trova le sue fondamenta nella fase di progettazione, a partire dalla quale, grazie all’implementazione dei principi di “Quality by Desing”(QbD), del “Quality Risk Management”(QRM) e dell’approccio “Science and Risk Based”, vengono definiti chiaramente gli aspetti critici di progetto su cui dovranno essere concentrati gli sforzi per le attività di Commissioning & Qualification.
La supervisione del reparto di qualità gioca un ruolo fondamentale nella fase di progettazione, poiché ha la responsabilità di assicurare che gli aspetti critici del processo vengano considerati durante la progettazione del sistema e la definizione dei test.
CDE (Critical Design Element)
Si pone l’attenzione quindi sulla definizione degli elementi critici di progetto, CDE (Critical Design Elements), che saranno oggetto dei test e che derivano da una attenta analisi degli attributi critici di qualità e dei parametri critici di processo definiti in fase iniziale di sviluppo, nonché dai requisiti regolatori e dagli standard di qualità aziendali.
Con questo approccio si abbandona la vecchia mentalità del “testare tutto”, per passare a quella di definire e pianificare dei test mirati e di conseguenza diminuire lo sforzo e aumentare l’efficienza sin dalle fasi di commissioning.
I documenti di Risk Assessment (RA) e Design Review/Design Qualification (DQ) in questo scenario diventano fondamentali e protagonisti, poiché consentono di indentificare chiaramente gli elementi critici di progetto, che attraverso il processo di Design Review portano a definire il progetto definitivo (1).
(1) Per approfondire: International Society for Pharmaceutical Engineering, ISPE Baseline Guide: Volume 5 – Commissioning And Qualification, 2nd Edition, Chapter 2, Paragraph 2.1 page 19, ISPE, January 2019, 212 pages
Risk Assessment
Una volta definiti chiaramente gli elementi critici della progettazione è fondamentale analizzarli nel documento di Risk Assessment, che ha come output la definizione e successiva esecuzione di test che portino da subito un valore aggiunto ai fini della qualifica.
Ad esempio l’esecuzione di test relativi alla fase di FAT, sviluppati secondo questo approccio, potrebbero portare alla luce difetti sulla realizzazione del sistema e ciò permetterebbe di poter agire velocemente apportando le correzioni in modo efficiente direttamente presso il costruttore e non in fasi di qualifica successive in cui sarebbe troppo tardi.
Allo stesso modo durante la fase di SAT potrebbero essere individuati eventuali difetti di installazione e funzionalità, legati ad aspetti critici di processo. Ciò favorirebbe un’azione tempestiva nella risoluzione, facilitando le fasi successive di convalida.
Design Review/ Design Qualification
Il processo di Design Review in quest’ottica gioca un ruolo importante durante la fase di progettazione, poiché, grazie al contributo degli SME del reparto di ingegneria che possiedono piena conoscenza degli attributi critici di qualità (CQA) e dei parametri critici di processo (CPP), va a definire in modo mirato, già nelle prime fasi, gli elementi critici di progetto (CDE) e le soluzioni di progetto adeguate.
Il risultato della valutazione dei rischi nel Risk Assessment e l’utilizzo dinamico della Design Review culminano nel progetto definitivo, il quale viene formalizzato nella Design Qualification (DQ) dove le scelte progettuali vengono confrontate con i requisiti specificati nelle URS per verificarne la piena copertura.
L’approccio appena descritto ci consente di evitare il presentarsi, in fase di test, di risultati non conformi che si riveleranno poi causati da errori di progettazione. Già in fase di FAT e SAT, con il nuovo approccio, si hanno test mirati alla verifica degli aspetti critici del processo, permettendo così una pianificazione ottimale delle fasi di Commissioning & Qualification e non avere perdite di tempo per test “standard” che non apportano nessun valore aggiunto.
Il ruolo del reparto di ingegneria, nella fattispecie degli SME, diventa quindi fondamentale per riuscire a definire sin da subito cosa andrà testato e dove concentrare gli sforzi di Commissioning & Qualification (C&Q).
Benefici
I benefici di questo modello sono molteplici, infatti nell’approccio di C&Q gestito attraverso il Quality Risk Management (QRM), tutte le attività di test, a partire già dalle attività di commissioning, aggiungono valore alle attività di qualifica, diversamente da un approccio classico in cui molte volte i test eseguiti nelle prime fasi di installazione del sistema (FAT, SAT e commissioning), che non sono stati definiti secondo un approccio orientato al rischio, risultano ridondanti ai fini della qualifica oppure, non essendo considerati perché non integrati nel processo di progettazione, vengono ripetuti in fase di IQ/OQ.
Nel nuovo approccio i test che vengono definiti sono commisurati ai rischi sulla qualità del prodotto, i quali vengono identificati, mitigati e controllati già nelle fasi di progettazione applicando le attuali GEP, ottenendo così come risultato la consegna di un sistema pienamente aderente alle specifiche, con costi ridotti e tempi più brevi.
References
International Society for Pharmaceutical Engineering, ISPE Baseline Guide: Volume 5 – Commissioning And Qualification, 2nd Edition, ISPE, January 2019, 212 pages.
EQUIPMENT & FACILITIES QUALIFICATION