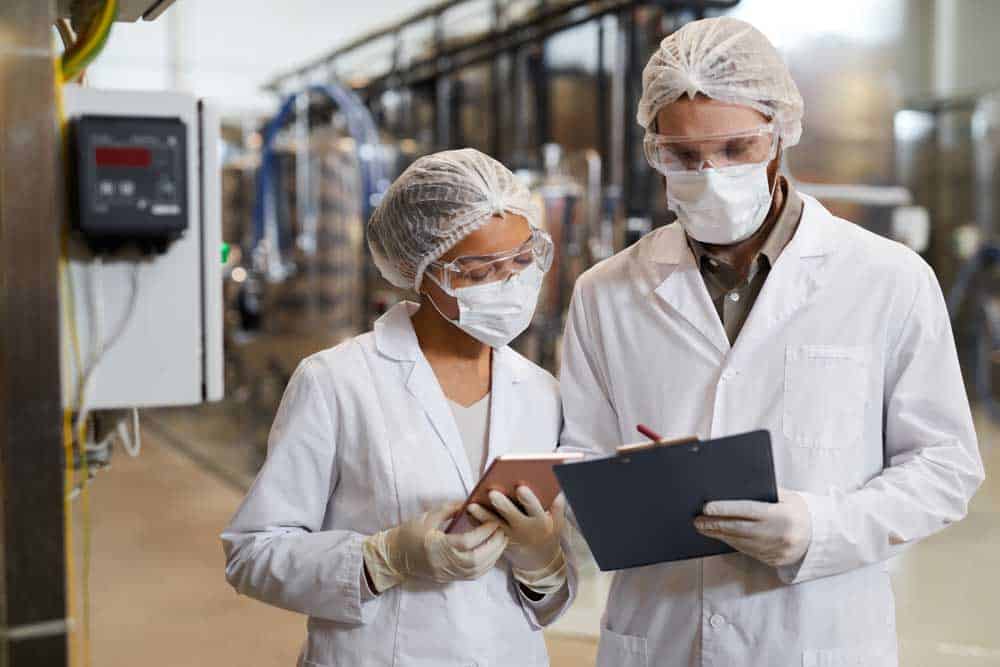
Discovering CAPA. Tools and techniques for optimising the process
Discovering CAPA. Tools and techniques for optimising the process
Discovering CAPA. Tools and techniques for optimising the process
Corrective and Preventive Actions (CAPA) are currently one of the major points of observation by the FDA.
The management of CAPAs is complex and difficulties do not always depend on staff shortages, but very often they are attributable to a problem in the structure and flow of the process. How often is it the case that not all actions are tracked, not all steps are documented or even data is lost in a cluttered system with excessively long implementation timeframes.
Furthermore, corrective action should be minimised as much as possible, as a consequence of deviations, non-conformities, etc., in favour of proactive approaches such as greater use of Quality Risk Management.
Being Proactive and Preventing is less expensive than being Reactive and Correcting!
In the following paragraphs, we will reference the regulations, explore tools and techniques to improve the approach to preventive and corrective actions, answer the most frequently asked questions about CAPAs and, finally, use an infographic to demonstrate how to simplify a CAPA process using a digital system.
Tools and Techniques to improve the approach to preventive and corrective actions
There are several techniques and tools that can be used to improve the approach to corrective and preventive actions.
The RCA uses different models and tools such as:
- Failure Mode and Effect Analysis (FMEA) is a methodology used to analyse the failure or defect modes of a process, product or system, assess the causes and evaluate the effects on the entire system/plant. Generally (but not necessarily) the analysis is carried out beforehand and is therefore based on theoretical and not experimental considerations. It allows organisations to anticipate possible defects and errors in process design during the design phase.
- The 5 Why method consists of asking the question “why” repeatedly until you understand all the symptoms of a problem and get to the root. The method is usually used during problem-solving activities or in conjunction with other tools, such as the cause and effect diagram.
- Ishikawa or fishbone diagram, so-called because it resembles a fishbone with a rectangle at the end containing the effect or problem. In manufacturing, the causes or factors influencing a production process are often organised into four macro-groups, which are: labour, machines (including the energy used and working and measuring instruments), materials (raw and auxiliary materials), and methods (operating procedures or practices). The Ishikawa diagram can be used as a support in brainstorming sessions with the team.
Despite strong regulatory pressures, not all deviations, complaints, audit results or supplier defects should trigger a CAPA. Trend analysis and risk management can help avoid the “everything is a CAPA” syndrome.
Trend Analysis: Paying attention to trends helps us understand whether a non-compliance is an anomaly or not and whether it therefore needs a CAPA process or simply corrective action following a deviation, etc. Trends can also identify minor issues before they become more risky, perform preventive actions and help to better prioritise non-compliances for further investigation.
Quality Risk Management (QRM). Quality Risk Management is a process to mitigate or eliminate risk. It starts with an initial assessment phase, up to a final periodic review. QRM is an increasingly popular process in the upstream inspection phase of any process and helps to reduce the number of open CAPAs.
The most frequently asked questions about CAPAs
What are CAPAs?
CAPAs (Corrective Actions, Preventive Actions) are a system of quality control measures designed to eliminate the causes of a deviation, non-compliance, defect or other undesirable situation in order to prevent its recurrence.
- Corrective action acts on existing non-compliances, deviations or defects.
- Preventive action is taken to eliminate the causes of a potential deviation, non-compliance or defect in order to prevent it from occurring.
Through a CAPA process, a company not only develops an Action Plan, but also determines, implements and monitors the effectiveness of an identified solution. Basically, through this process, the company Quality Control system is able to “self-correct” and improve itself.
Why open a CAPA?
The purpose of corrective and preventive actions is to acquire information, analyse it and identifyand investigate problems with quality in the product so ast totake appropriate and effective actions to correct the problem and prevent its recurrence.
Key to this process will be the testing and validation of corrective and preventive actions, the communication of activities to be carried out to the responsible parties, the documentation of activities and the collection and sharing of relevant information for management review.
When to open a CAPA?
CAPAs are opened following and in the presence of certain inputs. Including:
- Deviations
- Non-compliance
- Change Control
- Internal/External Audits
- Complaints
- Rejection of products
- Management Review
- Regulatory inspections
- Trends in process performance and product quality monitoring
Who opens the CAPA?
Usually the CAPA is linked to other “parent” processes such as Deviations, Complaints, etc., so the people who open CAPAs are those who have previously instigated another process. However, there are often committees within companies, which discuss the process and jointly decide who should be in charge of it. Quality Assurance is generally represented in the committees.
What are the reference regulations and guidelines for corrective and preventive actions (CAPA)?
The reference regulations for the management of CAPAs are:
- EMA ICH Q10 Pharmaceutical quality system
- ISO 13485:2016
- ISO 9001:2015
- FDA 21 CFR 820 Quality System Regulation
Although CAPAs are not specifically indicated in the cGMPs for pharmaceuticals (21 CFR 210 and 211), there are requirements that are parallel to the CAPA concept. It is clear that CAPA expectations have become a current GMP for pharmaceuticals.
21 CFR 211 (e.g. 21 CFR 211.160 and 211.192) contain requirements parallel to the CAPA requirements listed in the Medical Device Regulations (21 CFR 820) (1-2).
How do you manage a CAPA using a digital system?
PRAGMA4U is a modular and scalable Workflow Management System platform that digitises work processes in compliance with FDA and cGxP guidelines.
It enables companies to: have documentation that is protected, always up-to-date, organised and linked to the source processes; assign and implement workactivities directly on the platform; easily share information between departments; keep processes under control using KPIs; and compile reports and dossiers that will be useful for inspections.
The platform can contain multiple processes, creating a true digital map of the company. It also integrates with other systems, such as ERP, simplifying the compilation and updating of data.
MORE INFO
Subscribe to our newsletter
Increase your knowledge, join a community of professionals and stay up to date each week on the latest industry news.