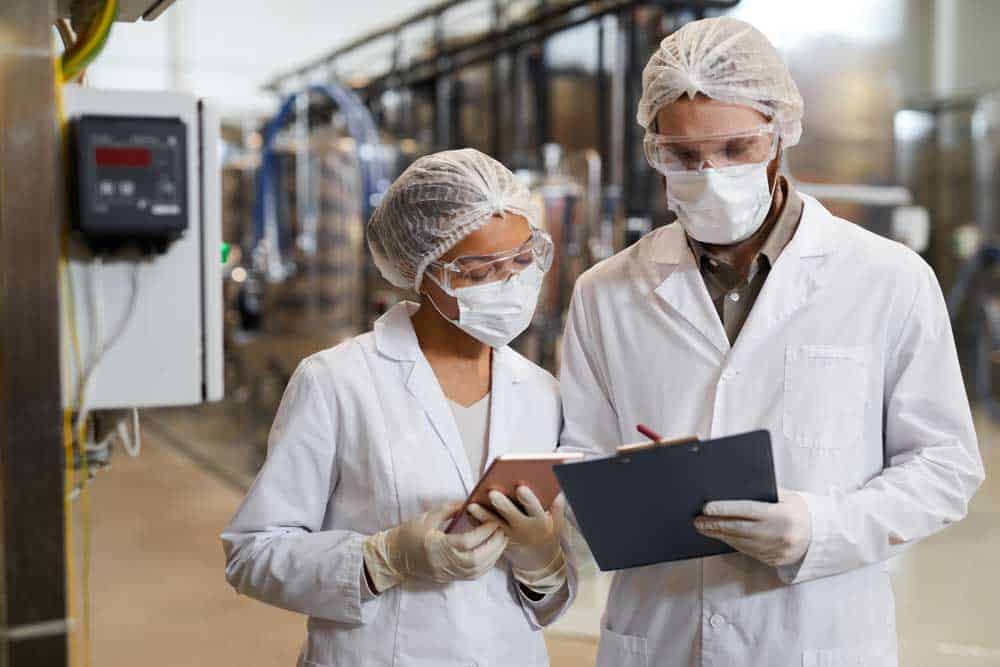
Pharmaceutical
A company that has always been engaged in the research, development and marketing of innovative drugs.
To validate a manufacturing process by reducing the risk of non-conformities and observations by the inspection authorities, while also achieving performance and quality objectives.
In accordance with the regulatory standards of the industry and the reference guidelines, the client company needed to study and validate the Hold Time for a pharmaceutical product
A preliminary assessment of the critical phases (granulation-mixing-compression-preparation of granulating and coating solutions) and associated hold times, based on the historical data of the product and the indications of the product data sheets for the raw materials.
Checking the impact on the cleaning validation of the equipment involved and on the establishment and definition of the validation documentation (protocol and production version).
Supervision of validation activities during manufacture, in accordance with the validation protocol (intensive implementation of the monitoring and sampling plan and in-process controls, required for critical process stages subject to hold time studies on product batches).
“On the job” training for the staff involved.
Collection and assessment of all analytical and process data for the definition of the maximum hold times for manufacturing intermediates, with the aim of ensuring a stable and reproducible process.
Drafting and definition of the final process report, together with issuance and definition of the new Time Control Sheet (a document that calculates and tracks the Hold Times between the various phases) within the Standard Production Version.
The S4BT consultants co-operated in synergy with various areas of the Client company, including Quality, Validation, Production and Engineering, for the entire duration of the project.
With the contribution of the skills of the S4BT professionals, the company completed the hold time validation for a specific process:
Client: a company that has always been involved in the research, development and marketing of innovative drugs.
Sector: Pharmaceutical
Objective: To validate a manufacturing process by reducing the risk of non-conformities and observations by the inspection authorities while also achieving performance and quality objectives
In accordance with the regulatory standards of the industry and the reference guidelines the Client company needed to study and validate the Hold Time for a pharmaceutical product, i.e. the period of time that may elapse between one processing stage and the next, during which it is essential to ensure that the physical-chemical properties of the product are preserved and microbial growth is avoided.
S4BT fielded resources with the skills and experience best suited to the characteristics of the project.
The team began by conducting a preliminary assessment of the critical stages (granulation-mixing-compression-preparation of granulating and coating solutions) and the associated hold times, based on the historical data of the product and the indications of the product data sheets for the raw materials.
They then focussed on verifying the impact on the cleaning validation of the
equipment involved and on the drafting and definition of the validation documentation (protocol and production version).
The team co-ordinated and supervised the validation activities during manufacture, in accordance with the validation protocol (intensive implementation of the monitoring and sampling plan and in-process controls, required for critical process stages subject to hold time studies on product batches).
The S4BT professionals then prepared specific “on the job” training for the staff involved, after which they collected and evaluated all the analytical and process data for the definition of the maximum hold times for the manufacturing intermediates, in order to ensure a stable and reproducible process.
Finally, the S4BT team focused on defining and drafting the final process report, and the issuance and definition of the new Time Control Sheet (a document that calculates and tracks the hold times between the various phases) within the Standard Production Version (a document that contains the processing instructions for a process).
With the contribution of the skills of the S4BT professionals, the company completed the hold time validation for a specific process:
Lorem ipsum dolor sit amet, consectetur adipiscing elit. Ut elit
Pharmaceutical Company
An international pharmaceutical contract manufacturer specialising in the clinical and commercial development and production of pharmaceutical products with a high degree of toxicity.
Digital Company
Lorem ipsum dolor sit amet, consectetur sit a sit fadipiscing elit. Ut elit tellus, luctus nec ullamcorper mattis, pulvinar
Petshop Company
Lorem ipsum dolor sit amet, consectetur sit a sit fadipiscing elit. Ut elit tellus, luctus nec ullamcorper mattis, pulvinar
Conditioner Company
Lorem ipsum dolor sit amet, consectetur sit a sit fadipiscing elit. Ut elit tellus, luctus nec ullamcorper mattis, pulvinar
Card Rental
Lorem ipsum dolor sit amet, consectetur sit a sit fadipiscing elit. Ut elit tellus, luctus nec ullamcorper mattis, pulvinar
Expedition Company
Lorem ipsum dolor sit amet, consectetur sit a sit fadipiscing elit. Ut elit tellus, luctus nec ullamcorper mattis, pulvinar
TOGETHER IS BETTER.
Simplify the management of Complaints, from filing, through investigation, follow-up, judgment and final report.
The module is designed to provide step by step Quality Assurance support
in the implementation and supervision of the process and the assignment of tasks to the departments involved. The module supplements the CAPA procedure, which the user can open directly from the Complaints procedure.
PRAGMA-WFM documents and traces all activities and information in the Complaints process. In each phase, you can also attach files in various formats to support activities and investigations.
During inspection phases, the functionality dossier enables the real-time generation of a document that provides information and lists the activities of the process and related processes
It simplifies the management of internal and external audits, from planning, through execution, to the management of remarks.
The module supplements procedures for handling CAPAs , Non Conformitiesand Change Control that the user can open directly from the audit to resolve the observations found.
PRAGMA-WFM documents and traces all activities and information of the Audit process. For each process step, it is possible to assign tasks to the people involved, and attach files in various formats.
Duringthe inspection phase, the dossierfunctioncan generate a document in real time which records the information and activities of the Audits and related processes